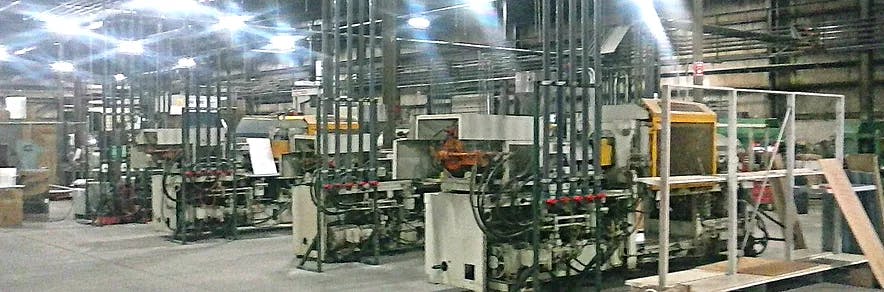
Discussion regarding aluminum to plastic conversions
All manufacturing materials possess different physical properties of strength, weight, conductivity, durability and a host of other properties that a manufacturer may deem important. Our discussion will focus on the viability of using extruded plastic in place of extruded aluminum in certain applications.
Plastic and aluminum can both be extruded or drawn into specific shapes desired by an end user. How this is done with plastic and similarities and differences to aluminum will be detailed here. PVC plastic will be used in the discussion as it is a material that is most often used in applications replacing aluminum.
What is PVC?
PVC (polyvinyl chloride) can be clear or colored, rigid or flexible, depending on the added compounds and final application that needs to be achieved. For example, there exists different PVC grades such as blow film, high impact, wire and cable grade, thermoforming, injection molding, rotational molding, etc.
How is it produced
The basic raw materials for PVC are derived from salt and oil.
Chlorine is manufactured by the electrolysis of sodium chloride, salt.
The electrolysis of salt water produces chlorine. The chlorine is then combined with ethylene that has been obtained from oil. The resulting element is ethylene dichloride, which is converted at very high temperatures to vinyl chloride monomer. These monomer molecules are polymerized forming polyvinyl chloride resin.
Additives can be added in the manufacturing process to change the qualities and properties of plastic. For example: rigid PVC like the one which is used in windows frames is normally PVCU ("unplasticized") or RPVC (rigid). On the other hand, flexible PVC is achieved by adding plasticizers such as phthalates.
In addition, pure polyvinyl chloride is unstable when exposed to visible light or UV. In order to modify this disadvantage and make it suitable for different applications antioxidants are added. Some other additives comprise:
Additives
Properties achieved
Anti-oxidants & other stabilizers
Slows the degradation rate by heat, light etc. , visible light or UV radiation
Compatibilizers
Enable PVC to be mixed with other plastics/recycling
Flame retardants
Reduce flammability of plastic
Pigments
To color the plastic
Plasticizers
To produce flexible plastic
Impact modifiers
To absorb shock without damage
Fillers
Inexpensive, inert materials that add bulk or structure to the plastic
Characteristics of Polyvinyl Chloride
These are some of the properties that makes PVC appropriate for several applications:
- Toughness, strength.
- Ease of blending, ease of processing
- Flame resistant and fire prevention properties
(For example PVC is difficult to ignite and in the absence of a powerful external flame will not continue to burn. This is due to its chlorine compound. This makes it an ideal construction and cable material.) PVC comes in fire safe formulas that comply with standards of FM 4910 or ANSI 4910 clean room standards. Noted flash points are @400-500 degrees
- It is compatible with other additives that can provide PVC clear or colored, rigid or flexible, etc..
- Excellent electrical insulation properties. This makes it ideal to be use in cables.
- Impact strength and resistant to bad weather conditions (i.e. it does not corrode and is very durable), appropriate to be used as a construction material (50% of all pipe in the US is PVC)
- Resistance to grease, oil and chemicals
- PVC is chemically stable and does not de-polymerize
- Thermoplastics can be re-melted and reused, although the purity of the material tends to degrade with each reuse cycle.
- PVC can be recycled The international standard for defining environmental claims on products or packaging can be found in ISO 14021: Environmental Labels and Declarations-Self-declared Environmental Claims.
For example, a recyclable plastic container using this labeling is marked with a familiar triangle with three arrows inside of it, which enclose a number giving the plastic type as follows:
1. PETE or PET (i.e. polyethylene terephthalate: thermoplastic material used in plastic soft drink and rigid containers)
2. HDPE (i.e. high density polyethylene: the plastic commonly used to make milk and water jugs and two liter soda bottle bases)
3. PVC (i.e. polyvinyl chloride)
4. LDPE (i.e. low density polyethylene: the plastic used in cellophane wrap, diaper liners, and some squeeze bottles)
5. PP (i.e. a light, thermoplastic resin used in packaging, coating, pipes, and tubes)
6. PS (i.e. polystyrene)
7. Others
Construction material
Due to PVC properties, as described above, around 50% of PVC (or vinyl) manufactured is used in construction replacing other materials such as wood or glass. Cost effective, resistant, good weather durability, etc.
PVC is strong, lightweight, durable and versatile. These characteristics make it ideal for window profiles. PVC's inherent flame retardant and excellent electrical insulation properties make it ideal for cabling applications.
It can be used for flooring, windows and door frames and shutters, water and waste pipes, electrical applications such as cable and wire insulation materials, architectural glazing systems, wallpaper, etc. Most replacements windows are vinyl.
PVC has been widely used for surgery, pharmaceuticals, drug delivery and medical packaging. Some products include blood bags, medical containers, fluid bags, tubing, heart and lung bypass sets, masks, gloves, bottles and jars, drainage systems, ducting, etc.
The reasons to use it in the medical sector is its safety and chemical stability and bio-compatibility, chemical resistant and low cost. In addition, it is usable inside the body and easy to be sterilized.
Automotive
Typical examples of PVC automotive components include: moldings, interior door panels and pockets, seat coverings, sun visors, seals, floor covering, wiring, exterior side molding and protective strips, anti-stone damage protection, etc.
Other applications
PVC can be used for manufacturing toys, packaging, electric and electronic equipment, household goods, coating, plastic parts in motor vehicles, office supplies, insulation and adhesive tapes, furniture, etc.
For consumers in shoe soles, children's toys, handbags, luggage, seat coverings, etc.
Industrial sectors for conveyor belts, printing rollers.
Electric and electronic equipment such as circuit boards, cables, electrical boxes, computer housing.
Material notes
Thermal Properties
The thermal insulating capacity of plastic is rated by measuring thermal conductivity (the transfer of heat from one object to another object with which it is in contact). Plastic is a poor heat conductor which makes it a good heat insulator.
This conductive capacity is measured in Watts Per Meter Kelvin (2W/mK). Looking at PVC and aluminum:
Rigid PVC is 0.16-0.19 W/mK
Aluminum is 150-190 W/mK
In other words, aluminum conducts temperature 150+ times better than PVC
Technical analysis of the calculation:
The k value, or Thermal Conductivity, specifies the rate of heat transfer in any homogeneous material. If a material has a k value of 1, it means a 1m cube of material will transfer heat at a rate of 1 watt for every degree of temperature difference between opposite faces. The k value is expressed as 1 W/mK. The lower this value is, the less heat the material will transfer.
This can be converted to an R value - Heat Transfer Rates (R & U Values) The two most common units used to evaluate the thermal properties of a material are U-value and R-value. The U-value is defined as the amount of conductive heat energy (BTU’s) transferred through a one square foot area for each one (1) degree temperature difference between the indoor and outdoor air. Units are BTU/hr/ft2/degree F. The lower the number the better the insulator. The R-value is just a different way of evaluating the thermal properties of a material. The R-value is the reciprocal of the U-value. R measures the ability of a given material (barrier) to resist the transfer of heat through a one square foot area for each one (1) degree temperature difference.
Units are Hr/ft2/degree F/BTU. Both units are per inch of thickness. The higher the number the better the insulator. Material U-Value R-Value Density, moisture content, etc. can have an effect on the U and R values shown above. As illustrated in the table below, cellular PVC is a better insulator than white pine or rigid PVC (i.e. vinyl siding). Also, the lower the density of the material the better the insulator. A lower density means more trapped air pockets within the core of the PVC board or sheet, which in themselves, are good insulators.
U- Value R- Value
White Pine 0.78- 1.3
Rigid PVC 1.02 – 1.45 0.69 – 0.98
Cellular PVC 0.48 2.1
Aluminum 1642 .00061
Technical analysis of R Value calculation:
Calculate the R-value by taking the reciprocal of the conductivity C to get R = 1/3.93 = 0.254 kelvin-meter^2/watt. You can also calculate the R-value directly as R = L/K = 0.305/1.2 = 0.254 kelvin-meter^2/watt
https://www.engineeringtoolbox.com/thermal-conductivity-d_429.html
Load Strengths
As noted previously, plastic comes in many different blends with many different properties. The same holds true of aluminum. In general, the load strengths of each material is measured by tensile strength of the material (the measurement of a material to breaking under tension)
Aluminum has a tensile strength of @ 40-45,000 PSI
PVC has a tensile strength of @ 7,500 PSI
For frame of reference, note that building codes usually require PVC handrails to have a tensile strength of 6,500 PSI. ASTM (American Society for Testing and Materials) Standard # D7032 - 10a states that vinyl or composite handrails must support a 200-pound load per lineal foot (supported).
A standard 8’ section of PVC that is .25” thick would be expected to bend no more than 1.50” at its center (unsupported).
Bacterial Resistance
Copper, silver and brass are antimicrobial (antibacterial + antifungal = antimicrobial), and these elements are often added to other compounds to inhibit bacterial growth. Copper and silver would be ideal in hospitals except for the fact that durability and maintenance would be huge undertakings. Stainless steel, aluminum and plastic, on their own, possess no intrinsic antimicrobial properties.
Aluminum needs to be anodized, to have a coating of deposited silver to be effective in inhibiting bacterial growth. Aluminum, in certain conditions, is prone to condensation, which necessitates a strong anodized coating.
Plastic can have additives added that make plastic antimicrobial. When added, its properties last the life cycle of the product. The additives are safe in the EU and approved by US EPA and are also food contact approved.
https://www.sciencedirect.com/science/article/abs/pii/S0257897202001500
https://www.ncbi.nlm.nih.gov/pubmed/30395430
https://linetec.com/specialty-finishes/antimicrobial-protection/
Properties of Plastic to Cleaning Agents
All disinfectants and cleaning are highly capable when wet. Their efficacy is measured by how much dirt they loosen while wet- to be wiped off, or how much bacteria they kill before drying up.
PVC can withstand any cleaning agent without damaging the part being cleaned. Agents that can damage PVC are acetone or methyl ethyl ketone.
Light sanding or use of acetone is sometimes used to remove a deep stain.
Scratch Resistance
In simplest terms, anything that scratches aluminum will scratch plastic. However, things that mar plastic may not necessarily mar aluminum. Similarly, aluminum will often dent while plastic will not. Aluminum must also be anodized to protect from possible corrosion and abrasion.
It is best to look at various parts of an automobile that contains aluminum, glass, rubber, steel and plastic for examples. Each material is used in automobile manufacture to exploit a property of the material. The plastic used as a bumper cover has different properties of rigidity and scratch resistance as opposed to a dashboard faceplate. This is due to additives. Plastic is formulated to perform different functions. In the plastics industry, the most common additives used are those used as:
UV inhibitors
Mold Release
Adding flexibility
Making plastic slippery (candy wrappers)
Torque release (bottle caps)
Lubrication
Anti-fog
Anti-static
Anti-scratch
Anti-microbial
Stiffening agents
Other Non-Specific Properties of Plastic
Workability – standard woodworking tools can be used with plastic. Sometimes plastic blades have more teeth to make a fine edge. PVC can also be chemically welded/joined to create one solid finished piece when joined.
Shipping weight – PVC is 60% of the weight of aluminum per cubic inch
Highly dielectric – PVC is an electric insulator not a conductor
Color – PVC can come in any color. PVC can also be stained
No anodizing – PVC parts do not need any secondary processes